Are you reprocessing your instrument containers correctly? – Part 2 Copy
Cleaning and decontamination processes
Container systems follow the same cleaning and disinfection processes as other reusable medical devices. First, used containers must be disassembled, and all disposable components discarded. External process indicators and locks, single-use filters and retention plates, silicone mats and liners are removed, and accessory devices are disassembled per IFU.
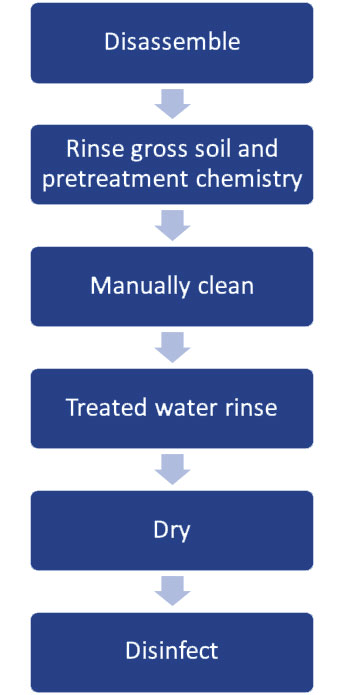
Next, all surfaces and accessories must be thoroughly pre-cleaned using a proper brush or sponge as directed by the container manufacturer. Remove and rinse out any excess debris, soil, and pretreatment cleaning product with the sponge or brush before the manual or mechanical cleaning process.
Manual cleaning may involve several steps, and every step must be completed. The cleaning methods and chemistries must be compatible with the rigid container system. Abrasive cleaning agents can cause corrosion or damage external surfaces of the container, which could cause cracking or degradation. For aluminum and plastic containers, a neutral pH detergent is often recommended to avoid the adverse effects of harsher chemistries.
Following manual cleaning, all components of the container system must be rinsed with critical water to remove detergent and soil residuals. After rinsing, they are dried with a soft, clean, lint-free cloth. If any residual soils or cleaning chemistry are found during visual inspection, the cleaning process must be repeated.
The disinfection step is necessary to make the containers safe to handle. To assure an effective process, it’s important to use compatible disinfectants formulated specifically for disinfecting medical devices and thoroughly removing cleaning chemistries.
Automated cleaning
Container cleaning can also be automated. Mechanical cleaning equipment cleans, rinses and thermally disinfects the containers. When using mechanical equipment to clean containers, end users must follow the system’s IFU and must use the required washer accessories to avoid negative outcomes or a lapse in the processing cycle. It’s also important to note that even if an automated process is being used, containers must still be disassembled and rinsed thoroughly per container IFU before they are placed in the automated system for processing. It may also be necessary to perform some manual pre-cleaning.
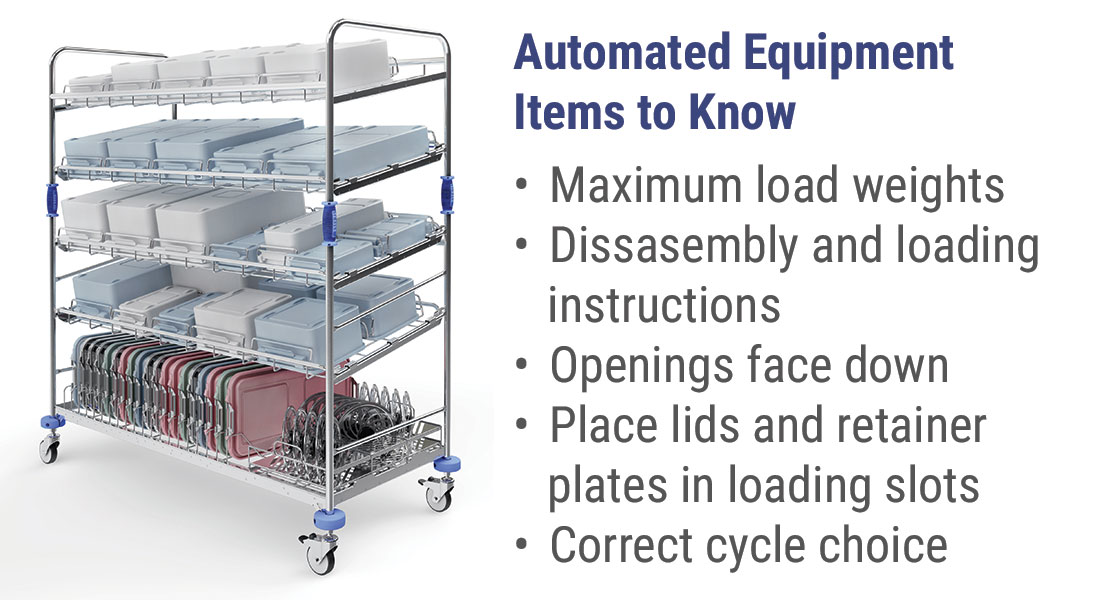
When loading containers into a washer-disinfector, it’s important to use the racks and other accessories designed specifically for processing containers in that system. Special racks are often needed to assure thorough cleaning of container systems and their accessories. Some washer-disinfectors use a single rack or basket, while others can have multiple shelves or baskets. Knowing how to load a rack is essential. Detergent can only clean what it reaches. Shadowing, stacking and other improper loading techniques block proper distribution of water and cleaning chemistries within the equipment, which prevents cleaning and thorough rinsing.
Automated systems often have impingement technology that disperses water and cleaning chemistries to all surfaces of the containers. Spray arms and nozzles increase the water pressure to apply force that dislodges residual soils. The programmed cycle used for containers is typically labeled “container” or “utensil,” but may vary depending on the equipment’s cycle names.
Cart washers come in an array of sizes to accommodate the needs of various sized facilities, from small ambulatory surgery centers to large hospitals. Using a cart washer to reprocess containers enables the department to improve its reprocessing workflows by not tying up smaller washer disinfectors with bulky containers. This frees up the washer disinfectors to be used for medical device sets and surgical accessories, which assures greater efficiency and throughput overall.