Description
By Susan Flynn, 3M Health Care
Has a new loaner tray ever given you pause because of its size, complexity, or density? Concerned about processing a new brand of container in your facility’s older sterilizers? Installing a new low temperature sterilizer? While the responsibility for validating sterilization parameters for reusable surgical instruments and packaging rests squarely with the device manufacturer, sterile processing professionals can and should perform product testing. Product testing can give you confidence that a particular instrument set or container can be successfully processed in your facility in your sterilizers. In fact, product testing is one of the four pillars of a comprehensive sterilization quality assurance program, albeit the one that is probably the least often practiced. This article will review the recommendations on product testing provided in national standards and guidelines.
Learning Objectives
- Review the four elements of a comprehensive sterilization monitoring program.
- Discuss approaches to streamline periodic product testing.
- Discuss AAMI and AORN guidance on the prepurchase evaluation of rigid containers.
About the Author
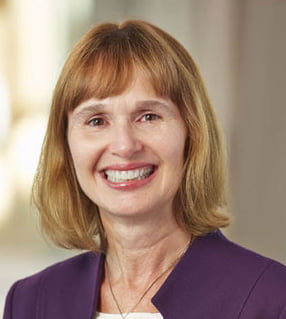
Susan Flynn has extensive experience as a Technical Applications Specialist with 3M’s Medical Solutions Division in St. Paul, MN, where she provided education for customers and sales personnel on improving the performance of the sterilization process and implementing best practices. Susan has served as a member of several AAMI Sterilization Committee working groups, and she has written on topics related to device reprocessing.